In the field of precision manufacturing, laser welding technology has become the core process in aerospace, new energy vehicles, 3C electronics and other industries due to its features of “high energy, high efficiency and low deformation”. However, the quality and stability of laser welding, but always around a key variable – temperature.
How to avoid material overcooking, weld porosity? How to ensure process consistency under different working conditions? The answer is hidden in the closed-loop temperature control system. Today, we take you to reveal the core principle and technical advantages of this technology.
First, the basic principle of closed-loop temperature control
Closed-loop temperature control system in laser welding is a real-time feedback-based control system, mainly contains the following core links:
- Temperature monitoring: real-time monitoring of the temperature of the welding area through high-precision sensors (such as infrared sensors or thermocouples).
- Data processing: the collected temperature signal is transmitted to the control unit, and the data is processed and analyzed through the algorithm.
- Control feedback: according to the set target temperature, the system dynamically adjusts the laser power, welding speed or other parameters to ensure that the temperature is always maintained within a reasonable range.
- Closed-loop control: forming a closed-loop mechanism of monitoring, calculating, adjusting and re-monitoring to realize high-precision temperature control.
Second, the key role of closed-loop temperature control in laser welding
1. Improve the welding quality
The quality of laser welding is extremely sensitive to temperature, closed-loop temperature control system through dynamic adjustment, can effectively avoid overheating or underheating caused by welding defects (such as porosity, cracks or welding is not solid).
2. Enhance process stability
Through real-time temperature feedback, closed-loop temperature control can significantly improve the stability of the welding process, reducing the impact caused by changes in material properties or environmental factors fluctuations.
3. Optimize energy utilization
Under precise control, the closed-loop system can reduce unnecessary energy waste, improve the efficiency of the welding system, while reducing production costs.
4. Support complex structure welding
For workpieces with complex shapes or uneven wall thicknesses, the closed-loop temperature control can flexibly adjust welding parameters to ensure welding consistency and uniformity.
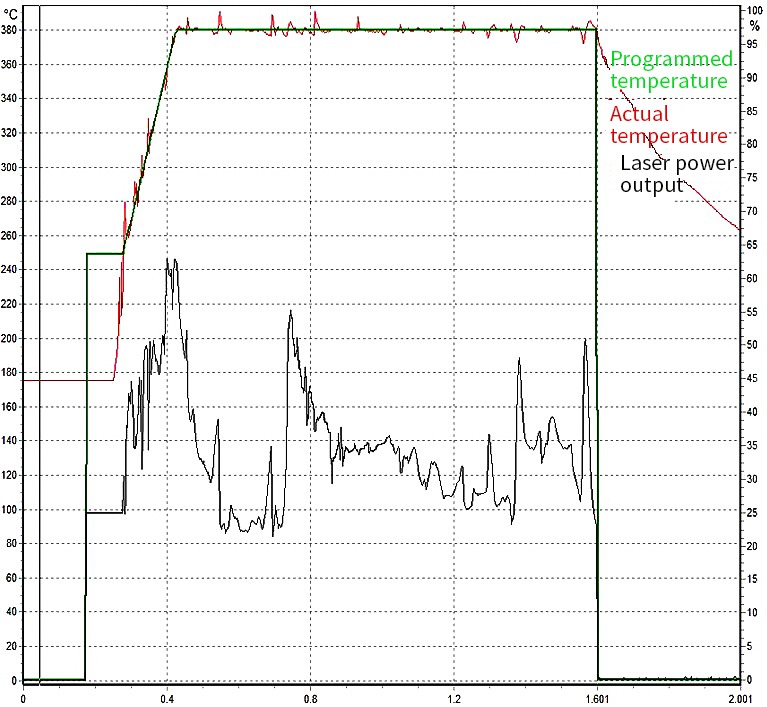
Temperature profile of DYNALAS' laser system under closed-loop temperature control
Third, the technical advantages of closed-loop temperature control
1.High precision control
Closed-loop temperature control system utilizes advanced temperature sensors and algorithms, which can realize microsecond response and high-precision temperature control to meet the needs of high-end manufacturing.
2. High level of intelligence
By combining with AI algorithm and big data analysis, the closed-loop temperature control can realize self-learning and intelligent optimization of the welding process, which can further improve the welding efficiency and quality.
3. Wide adaptability
The technology is applicable to a wide range of welding materials and complex welding environments, such as aluminum alloys, stainless steel and nickel-based alloys.
4. Easy to integrate and upgrade
Closed-loop temperature control systems are usually modularized, can be seamlessly integrated with industrial automation systems, and are easy to upgrade.
Fourth, the closed-loop temperature control technology application scenarios
1. Automotive industry: for body welding, power battery connection and other high-precision requirements of the application.
2. Aerospace: in the welding of aircraft structural parts, closed-loop temperature control can ensure the strength and consistency of the weld.
3. Electronic industry: package welding and micro-device manufacturing have very high requirements for temperature control, and closed-loop systems can meet such needs.
4. Medical equipment: In the manufacture of high-end medical equipment, closed-loop temperature control ensures the non-destructive and high-precision welding process.
Driven by the manufacturing demand of “high precision, high reliability and high automation”, the closed-loop temperature control has been upgraded from an “optional function” to a “core necessity” of the laser welding system. It is not only the “guardian” of process stability, but also the “propeller” of intelligent upgrading.
Choosing closed-loop temperature control means choosing the ultimate control of quality and the unlimited pursuit of efficiency.